Screen printing is the technique of pushing ink through a stenciled mesh screen to create a printed design, blending creativity and precision. The traditional yet dynamic method, revered for its versatility and vivid results, has become a cornerstone in the world of printing.
This article unpacks the vibrant advantages, diverse applications, and essential toolkit for screen printing, guiding you through the process step by step. It should help you figure out what is screen printing and determine if it’s the option for you—if not, we have a few alternatives to consider instead!
Table of contents
- Advantages of screen printing
- What is screen printing used for?
- Screen printing equipment
- Step-by-step guide to screen printing
- Screen printing options and alternatives
Advantages of screen printing
Let’s start with an eye-opening statistic: according to a report by Global Industry Analysts, the global screen printing market is on a trajectory to be worth US$11.2 Billion by 2030. Currently valued at US$3.5 Billion, this growth is a testament to screen printing’s enduring popularity. And it seems it will continue to be a top printing choice for years to come.
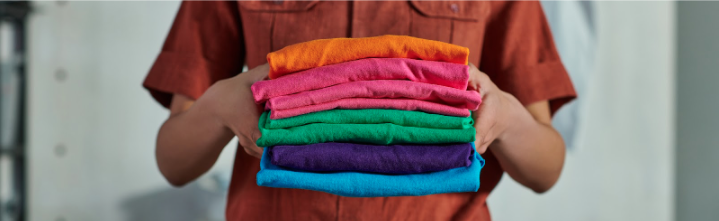
via DepositPhotos
And why, you might ask? Because it’s the go-to method for those who want more bang for their buck, more pizzazz in their print, and more life in their designs.
So, let’s look closer at why screen printing is so popular…
- Unmatched color brilliance: It produces exceptionally vivid colors, even on darker materials.
- Durability: Color vibrancy endures over time as if someone cast an anti-fading spell—ideal for designs that need to be resilient.
- Precise detail: The screen allows for sharp and accurate reproduction of intricate designs.
- Versatility across mediums: This printing method isn’t limited to just one type of material, but is adaptable to fabrics, wood, and glass.
- Tangible texture: The ink sits thicker compared to other printing techniques, adding a tactile feel and distinct texture to the printed surface.
- Cost-efficiency: When dealing with large orders, screen printing is the economical champion. The initial steep setup costs are smoothed out over a big batch of prints, making it cost-effective long-term.
- Eco-friendliness: With the growing availability of water-based inks, screen printing can be environmentally friendly, aligning with the increasing demand for sustainable printing solutions.
What is screen printing used for?
Let’s explore the array of applications where screen printing excels:
- Clothing: Vibrant designs screen-printed on clothing items, namely custom T-shirts, endure over time.
- Textile fabrics: Commonly used to print onto fabric, this technique is ideal for customizing tote bags.
- Merchandise: The precision and durability of screen printing ensures high-quality, consistent replication of brand colors and logos.
- Decals and stickers: Screen-printed decals and stickers are resilient against the elements and daily wear and tear. Designs remain intact and unfaded.
- Balloons: The thicker ink used in screen printing means the designs don’t distort or lose their shape when the balloon is inflated, maintaining the integrity of the print.
- Product labels: Resilient screen-printed labels can endure handling and the elements.
- Signage: Eye-catching screen-printed signs and displays create enhanced retail and exhibition visuals.
- Sports products: Screen-printed designs on sports gear can withstand extreme wear and tear.
Screen printing equipment
What you’ll need for screen printing
- Your design
- Item(s) you’re printing onto
- Screen printing press (manual, semi-automatic, or automatic)
- Acetate sheet(s)
- Printer (that can print onto acetate)
- UV exposure unit
- Mesh screen
- Photo-sensitive emulsion
- Scoop coater (to apply the emulsion)
- Ink of your choice
- Squeegee
- Washing fluid and station
Note: In this guide, we’re talking about the most common screen printing method of transferring a design onto acetate. If you decide to opt for a different screen printing method, the required equipment and specific steps will be different.
Screen options
Screen printing requires a specific type of screen, with varying mesh counts. Mesh count is measured by how many openings there are per square inch. The higher the mesh count, the smaller the openings and the more detailed the design. Different mesh counts are suitable for different projects, depending on the complexity of your design and the type of ink you’re using.
- Low mesh count (e.g. 38-86, 85-110): Ideal for printing bold images with heavy ink deposits—like glitter or shimmer inks—and for simple designs on darker fabrics.
- Medium mesh count (e.g. 110 or 156, 155-160): The go-to for general screen printing projects, suitable for detailed designs using standard plastisol inks.
- High mesh count (e.g. 230 or 305): This count is excellent for printing intricate designs with fine details and halftones. Used for thinner ink applications, such as water-based or discharge inks.
- Ultra-high mesh count (e.g. 355, 380, or 400): Reserved for extremely detailed designs and very thin inks. Produces a softer hand feel on the fabric.
Emulsion options
- Diazo emulsion: Versatile, durable, and ideal for detailed work. However, it has a longer exposure time and sensitizer is required.
- Photopolymer emulsion: Pre-sensitized, with fast exposure and high resolution, but has a shorter shelf life and higher cost.
- Dual-cure emulsion: Mix of Diazo and Photopolymer traits. Good for various jobs, with a moderate exposure time.
Ink options
- Plastisol ink: Ideal for most standard screen printing on fabrics. Popular for its ease of use and vibrancy. Requires heat curing.
- Water-based ink: Softer hand feel, eco-friendly, and ideal for light fabrics. Requires thorough drying.
- Discharge ink: Works best on dark, 100% cotton fabrics and offers a soft, vintage look. Removes existing fabric dye.
- UV ink: Cures quickly under UV light. Suitable for non-textiles, such as plastics and metals.
- Solvent-based ink: Durable and adheres to various materials. Used for industrial applications.

Design by green in blue via 99designs by Vista
Depending on the result you’re aiming for and the item you’re printing onto, you might also consider specialist inks. For instance, glittery, textured, or puff inks create distinctive visuals, tactile experiences, and raised surfaces.
Tip: If you’re looking to screen print on garments, opt for heat-treated inks that become machine washable and colorfast post-curing.
A step-by-step guide to screen printing
Find out how to screen print from start (collecting all the equipment you’ll need) to finish (removing the emulsion and delighting in the final product).
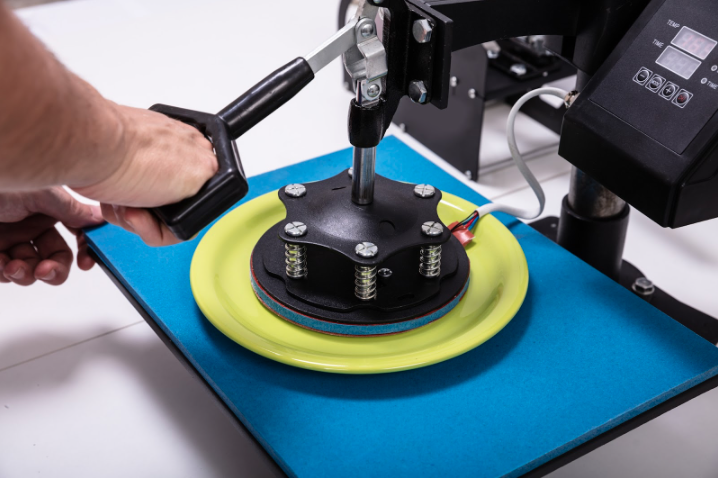
via DepositPhotos
Step 1: Create a stencil
First, you need to create a stencil of your design, which you will then transfer onto your chosen surface.
The most common and contemporary method uses a photo-sensitive emulsion to transfer the stencil onto the screen. For this method, print your design onto an acetate or Mylar film sheet. Alternatively, you can hand-draw your stencil onto the acetate with opaque ink or use Rubylith, a masking film that blocks UV light.
For multi-colored or multi-layered designs, you will need to create a seperate stencil for each color or layer. If you’re a screen-printing novice, perhaps start with a simple design with one or two colors.
Tip: For a more freehand approach that doesn’t require a printer or a UV exposure unit, you can paint or place your stencil directly onto the screen. However, prints created this way will provide a lower level of detail and the final design will be an inverse of the original i.e. negative space will become positive, and vice versa.
Step 2: Prepare the screen
To transfer your stencil onto the screen, first you will need to prepare the screen with photo-sensitive emulsion using a scoop coater. Fill the scoop coater with your chosen emulsion and, holding it against the screen at a slight angle, drag the metal trough smoothly and evenly up the screen. Ensure the emulsion covers the entire surface without overloading it.
Step 3: Expose the emulsion
Now it’s time for the exposure process. Once the emulsion has dried, lay your design onto the coated screen and place the screen in an exposure unit that emits UV light. Exposure time depends on the type and thickness of the emulsion, the mesh count, and the exposure unit you’re using.
Here’s how it works: the design on the acetate sheet blocks the UV light, preventing the emulsion in those areas from hardening, while the exposed emulsion hardens. This creates the stencil through which ink will pass during the printing process.
Tip: While exposure units are common in professional screen printing setups, they can make the DIY process feel less accessible. If you don’t have access to an exposure unit, don’t worry! You can use simpler methods like placing a physical stencil directly onto the screen or hand-painting the design using opaque ink.
Step 4: Wash off the emulsion to reveal your stencil
After your screen has been exposed, gently rinse it with water to remove the soft emulsion, revealing your stencil design! Thoroughly dry the screen while checking for any small mistakes, ensuring the stencil matches your original design perfectly.
Step 5: Press the ink through the screen, applying your design
Place the screen onto the printing press and the item you’re printing on (a T-shirt, for example) onto the printing board underneath the screen, making sure it’s flat and properly aligned. Holding the squeegee at an angle, pull it firmly down the screen using consistent pressure. Lift the press slightly, and push the ink back to the top of the screen using the squeegee. Known as “flooding the screen”, this is a necessary step for inks that may dry in the mesh, such as water-based inks.
If you’re printing a batch, simply lift the screen, set a new item on the board, and repeat the process.
Step 6: Remove the emulsion and dry
Once you’ve finished with this stencil, it’s time to clean the screen. Apply a special washing fluid to dissolve and remove the emulsion without damaging the mesh.
Your screen is now ready to have a new stencil transferred onto it, should your design incorporate more than one color or layer. Thoroughly remove the emulsion between each new stencil you transfer and print, repeating each step of the process.
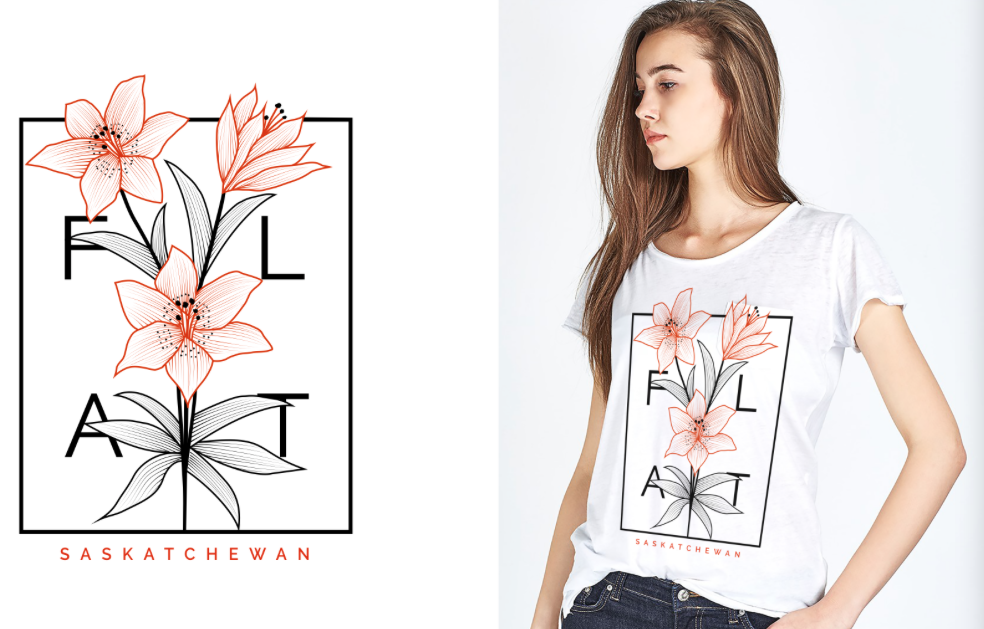
Design by Skilline via 99designs by Vista
Make sure each layer has dried properly before moving on to the next. Once your prints are complete, inspect the final product and leave to dry.
What are my screen printing options and the alternatives?
6 key types of screen printing
- Spot color screen printing: Using individual solid colors for each part of the design, this method is ideal for bold, simple graphics.
- Halftone screen printing: Utilizing dots of varying sizes and spacing to create gradients and shading, this technique is perfect for detailed, photorealistic images.
- Grayscale screen printing: Works exclusively with shades of black and white to produce various tones and contrasts, creating a monochromatic effect.
- Duotone screen printing: Using two—often contrasting—colors to create depth and dimension, adding a creative twist to simple images.
- CMYK (4-color screen printing): Combining Cyan, Magenta, Yellow, and Key (black) inks to create full-color images. This method is suitable for complex, multi-colored designs.
- Simulated process printing: Blending various inks to simulate the full spectrum of colors, and often used instead of CMYK on darker garments, this technique is used for detailed, multi-colored designs.
What is the difference between screen printing and heat transfer?
Heat transfer involves printing a design onto special paper and transferring it onto the material using heat and pressure. This method is better suited for small batches and complex color designs but is generally less durable than screen printing.
What is the difference between screen printing and digital printing?
Digital printing directly applies ink to materials using computer-controlled printers. While screen printing excels in longevity and color vibrancy, digital printing provides a quicker turnaround and flexibility for intricate, multi-colored, complex designs.
Can I outsource my screen printing project?
Thinking of printing your design using the dynamic screen printing method but feeling overwhelmed by the process and equipment? No worries, you don’t have to go it alone. Services like VistaPrint are here to rescue you from the nitty-gritty of DIY. We’ve got the tools, the team, and the know-how to bring your vision to life; the perfect solution for anyone who wants the dazzling quality of screen printing without the fuss of doing it themselves. With VistaPrint, you get professional results, time savings, and peace of mind, all wrapped up in one convenient package.
Ready to make your own screen-printed design?
Check out all your screen print options and bring your product to life today! Tell me more.